Contents
What is needle press
Needle pressing is a form of surface decoration of printed products by pressing on the printed surface to be emphasized such as images of patterns, letters, logos, symbols, brand names with gold, silver or other colors. aim to make the product more prominent. Using a heated printing mold, forcefully press the emulsion sheet into the printed product. Thanks to the heat and pressure, the emulsion is pressed into the printed product where the printing mold protrudes.
The advantages of Ep Kim
- Increase product aesthetics. Metallurgy will create an iridescent metal layer on the surface of the product, with beautiful, sharp, non-smudging and eye-catching colors. In particular, needle pressing will be sustainable with the time the product has a high aesthetic value. Metallic details in the product have a special effect that catches the attention of customers. Depending on the product design, customers can choose suitable metallurgical colors, metallized colors are very rich such as gold, red, blue, silver, purple, brown …
- Add value to the product. Thanks to the needle pressing technique, the product becomes much more advanced. In particular, with products that are meticulously and carefully designed and printed, beautiful packaging will evaluate the products inside. This will be the factor that leads to the purchase decision of the customer. With high-end, valuable products, people rarely consider calculating, without hesitating to spend heavily.
- Make a good impression on your customers. At first sight, customers will have more sympathy for the product, when details such as logos, brand names or patterns are prominent. That is the correctness in the image, customers can feel the effort of the invested business and they appreciate the products they create. Such a product can not be inferior quality.
Outstanding Advantages of UV Ink
Currently, UV inks are gradually gaining popularity and are used more and more in printing. The use of UV ink brings many obvious benefits to the product in terms of both aesthetics and durability. However, there are also many cases of difficulty in using UV ink because of problems related to adhesion. Let’s learn these factors with DKT VIETNAM.
UV ink is a product used to cover the surface of materials and is cured by UV rays. The curing process is the factor that creates the outstanding advantages of UV inks. Specifically, ink when exposed to ultraviolet light will change from a liquid or viscous form to a solid form. At the same time, the compounds in UV ink also have differences, forming their unique characteristics.
- UV ink increases the aesthetics of the product, the surface of the product is glossy, sharp, and the color is uniform.
- The ink has good adhesion on many materials, including “difficult” surfaces such as glass, marble, etc.
- The ink layer dries instantly, facilitating quick system operation, shortening waiting times, and improving work efficiency.
- The ink film is very resistant to chemicals or mechanical impacts. As a result, increased resistance to scratches and abrasion caused by external factors helps protect the product.
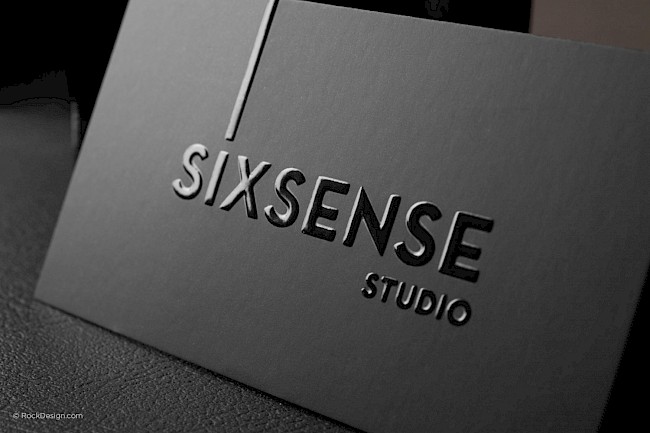
What is UV coating?
UV coating is a type of chemical containing: Oligomer, Monomer, UV Photoinitiator and some other additives. After being coated on paper and dried immediately by UV UV light for a very short time of about 2-3s.UV coating can vary in reflectivity, thickness or depending on the application. use different UV effects such as: sandblasted, grainy, glossy, matte… There are 2 types of UV coatings: oil-based UV and water-based UV.
- Oil-based UV: is an oil-based type that is dried by UV ultraviolet light. They have high gloss, scratch resistance, abrasion resistance, water resistance much better than water-based. This helps to better protect the surface of the product.
- Water-based UV: A water-based type that is dried by IR infrared heat drying. Compared to oil-based UVs, they are also glossy and matte, but the gloss is not as high. At the same time, scratch resistance, water resistance is also much worse than oil-based.
Why is UV coating difficult to cure?
- Irradiation intensity of UV rays: The curing mechanism of UV is different from that of traditional hot glues. Only points that receive UV radiation will react. Therefore, the more UV irradiation, the faster the reaction, the better the effect. Therefore, the converging glass of the lamp must ensure to focus all the emitted UV rays to reach the surface of the film to be cured. Lamp intensity is guaranteed at a minimum intensity of 80W/cm.
- Infrared Irradiation: When we talk about infrared, we usually think of heat. In the curing mechanism of UV, temperature has a good influence on surface smoothing and reaction rate. However, for heat-sensitive materials, infrared is a disadvantage. Therefore, in the design, it is necessary to minimize the infrared rays shining on the surface of the material to be cured.
- Thickness of coating: In the coating film, the photosensitive agent is evenly distributed, but if UV rays cannot reach, the resin underneath is not fully reacted, causing the adhesion to decrease. The thicker the coating requires the stronger the light intensity, the higher the amount of illumination must also be.
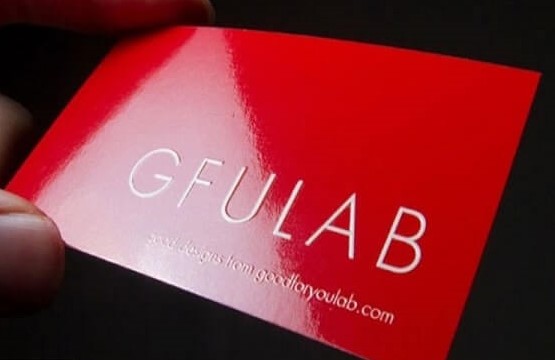